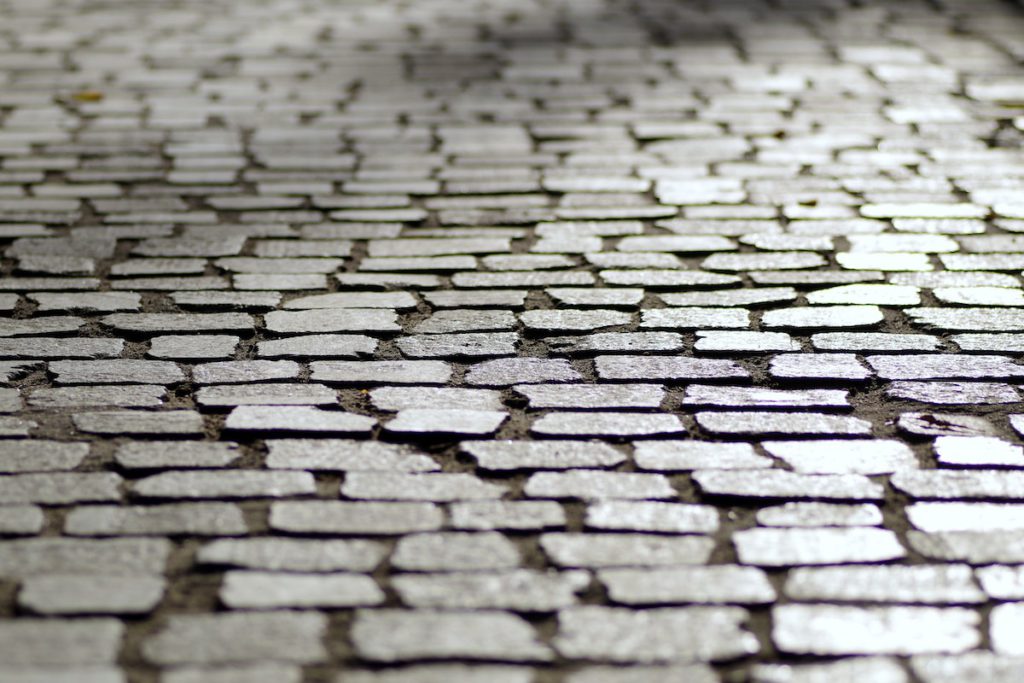
Fired clay bricks are the most commonly used building materials worldwide. The attractive physical, thermal, and mechanical properties of fired clay bricks make it an ideal material to construct buildings. Particularly because of its longevity, compactness, and durability. These changes in microstructure and brick composition would adversely affect the material’s mechanical resistance. Many studies have been conducted to discover ways of improving thermal conductivity in fire-resistant clay bricks. One being the recycling of waste materials composed of higher organic content.
A series of studies on recycled wastes in fired clay bricks have been conducted to examine the relation between additive usage in fired clay bricks and micro-pores and nano-pores formed therein. Now, a team from RMIT University, Melbourne, Australia, has demonstrated that fire-clay bricks that include biosolids. It can become a sustainable solution for both wastewater treatment and the brick manufacturers in Australia. The study shows how making biosolids bricks requires just about half as much energy as traditional bricks.
The study also showed that the fire energy requirements for bricks were reduced by as much as 48.6% for bricks that included 25% biosolids. It was found that the higher energy consumed in the burning process, the higher the thermal conductivity of fired clay bricks. In the present study. Fired clay bricks were manufactured from 0.5%, 1%, 1.5%, and 2% CB in bulk. It was tested compared to the control bricks of 0% CB.
Calcine furnaces were used to burn the ingredients, which were pulverized as goo, and added to the clay bodies. Muffled kilns were used for enamelling ceramics, or for firing decorative designs on ceramics that had already been enamelled. Wood burning kilns are not as common today but were one of the oldest methods for making ceramics. These kilns were typically built by a ceramicist using bricks or were designed to resemble an igloo or a small cave. Like the wood-burning kilns, soda kilns are made of bricks, usually big enough for one person to fit inside.
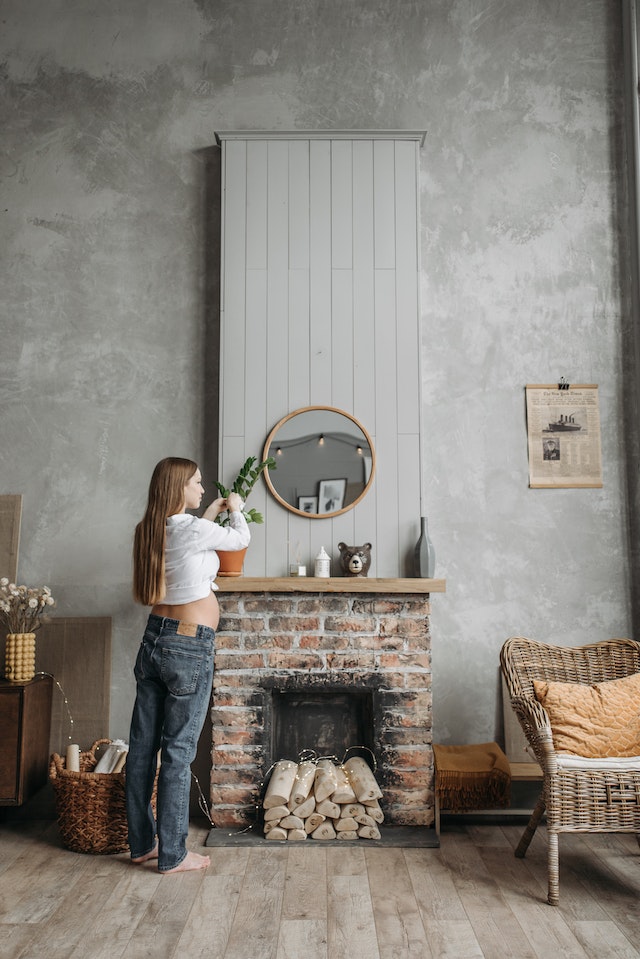
Electric kilns are lined with insulating brick, and depending on which style they are, they may load either top-down or bottom-up. Electric kilns are robust and fairly easy to operate, particularly because you can set up a kiln to burn your pieces according to a schedule. As such, electric kilns are generally not used in the process of firing raku. Instead, a kiln is sealed off on entry whenever a kiln is fired. Oxidation firing is where the kiln has an adequate oxygen supply during firing. The amount of oxygen in the kiln will influence how clay and glazing look after firing.
Pit-fired firings use fuel, just as do other kilns that burn fuel. Pit firings and sawdust kilns are sometimes made from metal drums, hardly a primitive material. As in the case of pit burning, the alternative structure for a sawdust kiln is the use of metal barrels. Sawdust burning involves building the kiln yourself from bricks or stones placed together. Pit-fired is still a popular, low-tech method for baking clay, and so are sawdust kilns. Remember, making masonry is more of an art form than a science. It is likely you will need several attempts before perfecting your signature recipe.
Beehive kilns are larger brick structures used in the industrial-scale manufacture of pottery. Gas kilns may be used for salt or soda fire. It results in a variety of textures and colours when compared to pieces fired in electric kilns. Bricks then need to be fired, or burned, in the kiln, to provide their ultimate hardness and look. After shaping or slicing, bricks have to be dried. in the open air in dry sheds, or in special drying kilns. The walls are made from baked clay bricks, cemented together by mortar made from sand and clay, and plastered over with further clay.
Mud is abundant and dirt-cheap as is the sunlight used to cure the clay bricks until they are firm enough to build on. Bricks were made at the clay pits of early times, which were returned to farming uses once the clay layers were exhausted. Biosolids-enriched bricks passed compression-strength tests, and analyses showed that the heavy metals were mostly trapped inside the bricks. Using at least 15% biosolids content in 15% of the bricks produced would consume up to this 5 million tonnes.